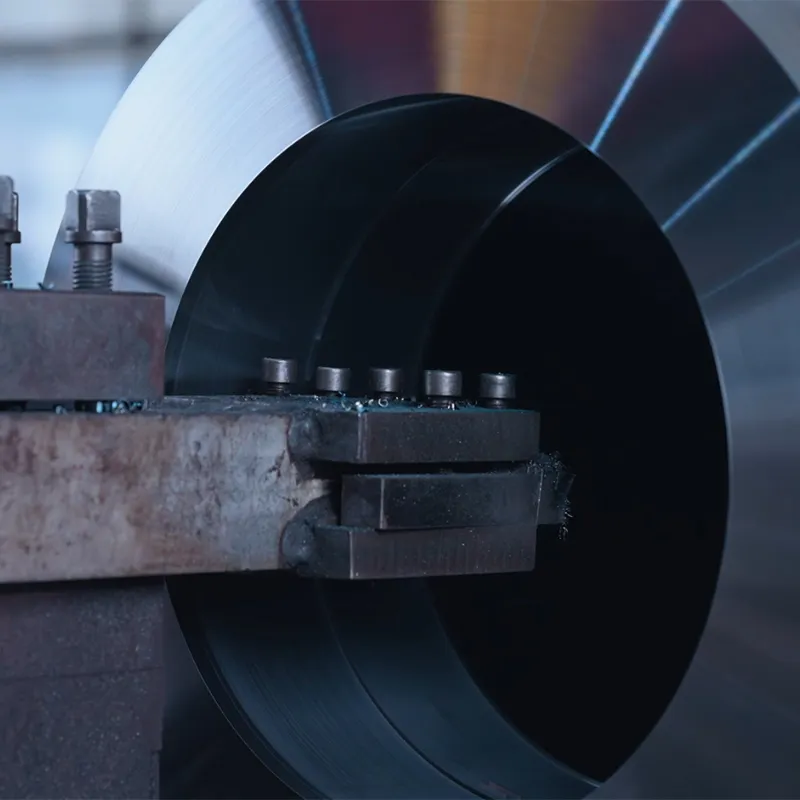
- Coating options: We provide hard chrome and tungsten carbide coatings, offering excellent wear resistance and long-lasting performance for corrugating rolls.
- Machining size: Custom machining is done strictly according to customer drawings, ensuring precise specifications and a perfect fit for every requirement.
- Flute profile selection: We work closely with customers to assess and optimize flute profile structures, enhancing both economic performance and efficiency. This process is applied to both new and repaired rolls, with options including A/B/C/E/F/N flute profiles.
- Heating methods: Choose from siphon pipe or peripheral heating systems to suit your production environment, ensuring efficient heat distribution and energy savings.
*Note: We provide customized corrugating rolls, pressure rolls, glue rolls, and doctor rolls for all brands, including BHS, Fosber, Mitsubishi, BW Papersystems, Marquip, Peters, Isowa, J.S., TCY, West River, Hsieh Hsu, K&H, XHL, Fuli, Wanlian, and more.
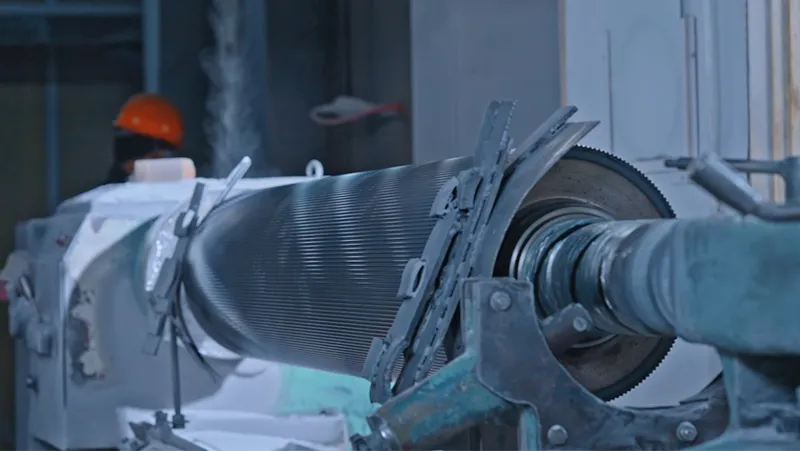
- Provide the blueprints or the specific brand and model of your equipment.
- Share your flute profile requirements, such as flute height and other specifications.
- Detail your production needs, including cardboard thickness, material properties, and production line speed.
We will provide you with specific customization recommendations based on the information you provide.
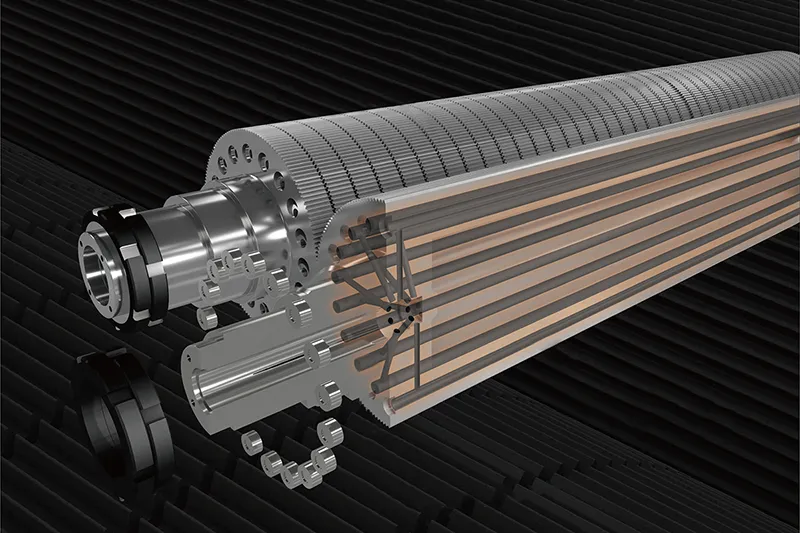
- Engineered for high-speed operations, capable of achieving up to 400m/min, ensuring efficient production.
- Durable and low-noise performance; the tungsten carbide corrugating rolls with peripheral heating are designed to last over 100 million meters, providing long-term reliability.
- Offers cost savings of 3-5% for customers, thanks to reduced waste paper and a UV-shaped flute design that cuts glue consumption, all while maintaining consistent flute height and pitch.